New Hampshire Advanced Manufacturing Partnership Internship at the John Olson Advanced Manufacturing
- Marguerite Kennish
- Jul 16, 2020
- 3 min read
Summer 2019
Edited by Elizabeth Mamros
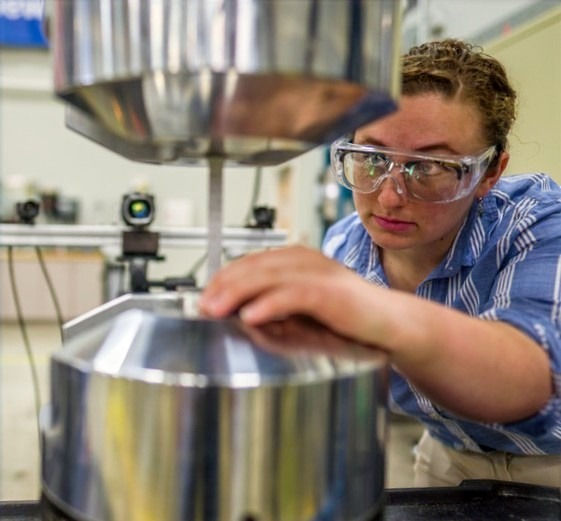
Metal Deformation Internship
The New Hampshire Advanced Manufacturing Partnership research internship held at the John Olson Advanced Manufacturing Center (Olson Center) was an amazing way to establish engineering experience. I spent the summer participating in a variety of hands-on learning opportunities and building strong foundational skills to apply in my first year at a four-year university, starting fall 2019. The skills I earned through the program prepared me for industry work and gave me an advantage in Introduction to Material Science class, and Mechanics of Materials class.
Developed Skills:
Exposure to good experimental practices and scientific publications
Introduction to MATLAB and SOLIDWORKS
Experience with Digital Image Correlation (DIC), VIC SNAP, and Material Testing Systemss
Research
The internship focused on studying metal deformation, by conducting a series of uniaxial tensile tests on stainless steel (SS316L). The steel was cut into dogbone specimens in 15-degree increments from 0-degrees (parallel, along the rolling direction) to 90-degrees (perpendicular). Sheet metal rolling fabrication causes elongated grains along the rolling direction. Elongated grain direction can cause anisotropy. Anisotropy is when a material exhibits varying reactions under loading, depending on specimen orientation. The changing specimen orientation allowed us to test if the material is anisotropic or isotropic (consistent material properties in all directions) behavior.
DIC is used to measure engineering and true strain. The video shown above is an accelerated uniaxial test. The analysis uses a changing scale, displaying the true strain that the material is experiencing. Throughout the clip the highest true strain areas are shown in red, and the lowest true strain values are in green.
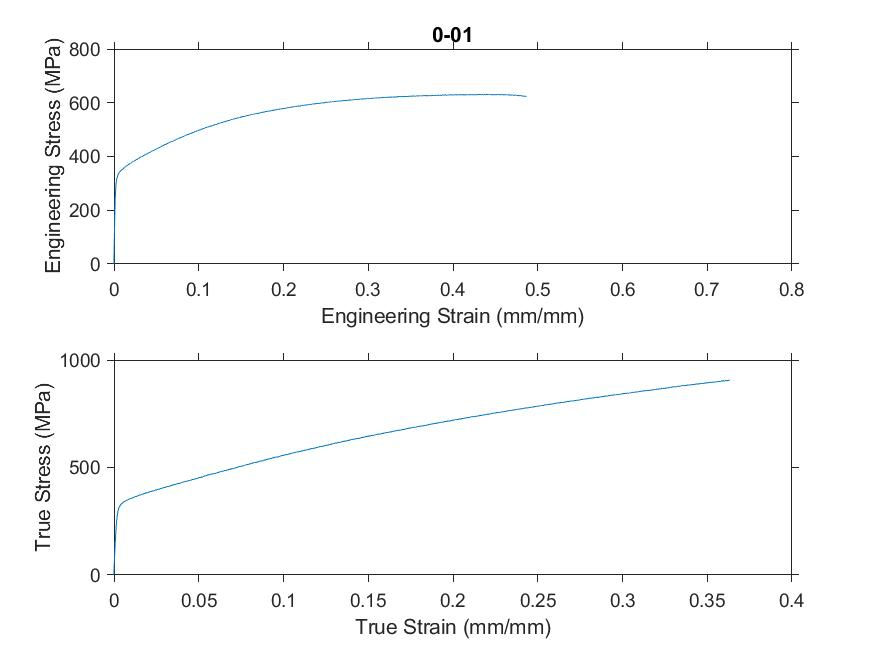
The force was recorded by the data acquisition device, as volts and is used to calculate the engineering stress. The engineering stress and engineering strain values are manipulated to calculate the true stress. I utilized MATLAB skills to plot the engineering and trues stress strain curves (right).
These curves allow researchers to better understand numerous mechanical properties, such as the Young’s modulus, the ultimate strength, etcetera. The results can help researchers to determine accurate material parameters for simulation calibrations.
Reflections
My friends and mentors, Elizabeth Mamros, a graduate student, and Ali Davarpanah, a postdoc, were incredibly supportive. They helped me to better understand research and gain systematic problem solving skills, which are essential to engineering . With their advice and guidance, I was able grow into a more well-rounded, advanced student.
Through this internship I met Professor Brad Kinsey from the Mechanical Engineering Department and Materials Science Program at the University of New Hampshire (UNH). He is a fantastic advisor and demands the highest quality of work from his apprentices.
I applied to the NH AMP research internship because of the accessibility to on-campus faculty. It also allowed me to build relationships with other student researchers before attending UNH. As part of the internship I attended weekly Olson Center meetings. In those meetings interns and students would take turns presenting our progress. Through those meetings I learned more about the other researchers and broadened my understanding of several mechanical engineering topics.
The program gave me the tools to better grasp my own motivations for entering the world of engineering. Through NH AMP I was able to push myself beyond earning a grade. They encouraged me to pursue a deeper understanding of complex concepts, beyond what a classroom lecture can offer. I wanted to push myself outside of my comfort zone, both socially and academically. This internship was the best platform to take that leap.
As of summer 2020, I am continuing to work remotely at the Olson Center. I am writing MATLAB code to automate the post-processing of future metal deformation tests for NH BioMade a $20M/5-year NSF EPSCoR award. Thanks to the internship the NH AM Partnership provided for me last year, I was prepared to teach myself complex coding techniques to help further our team’s research.
Kommentare